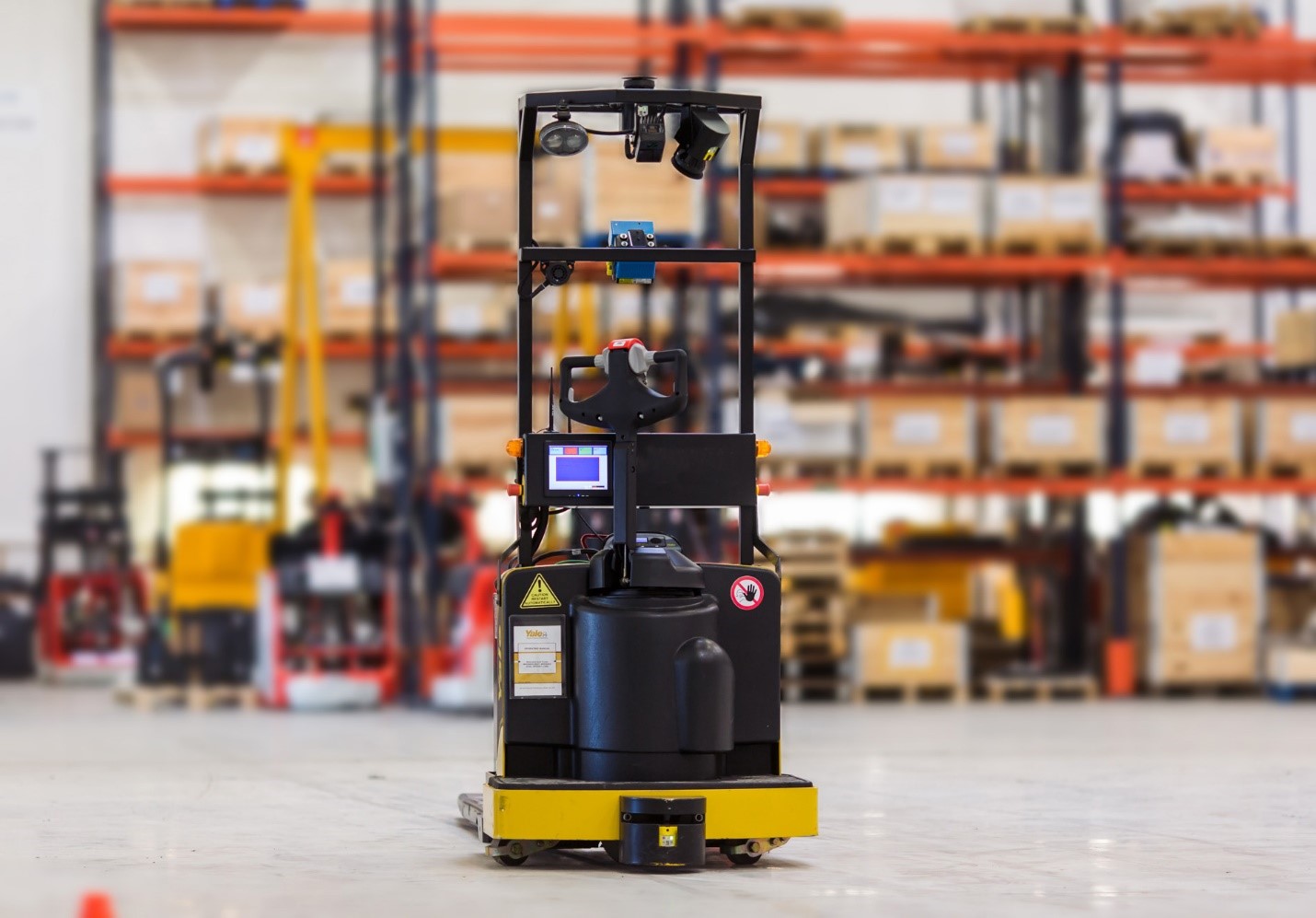
Robotic lift trucks (RLTs) are growing in popularity for applications in warehousing and manufacturing, and for good reason. With warehouse turnover well over 40%, operations are turning to robotics to relieve their dependency on a transient labor pool, reduce operating costs and help increase efficiency as they strive to meet escalating demand for high throughput and fast delivery.
While not every situation is right for robotics, technology has advanced to accommodate a range of horizontal transportation and vertical storage tasks in many environments. RLTs are especially well suited to handle repetitive tasks and long runs, a valuable characteristic warehouses can use in strategies to help curb operator turnover.
By shifting certain applications to robotics, companies can focus their employees on more engaging, value-added tasks that require human judgement – leaving the non-stop, tedious, back-and-forth load moving to robotic lift trucks. Automating transportation tasks can also play a role in limiting the chances of a safety incident, as it can avoid workflows that require employees to frequently traverse congested lift truck and pedestrian traffic areas.
To realize the greatest benefit, warehouses should evaluate which of their facility’s applications are the best fit for automation.
-
From production line to storage or shipping
Finished goods need to move quickly to a storage or shipping area. These jobs are usually repetitive, longer hauls that can take two minutes or more per load. When products come off a palletizer or stretch wrapping system ready to be picked up, a warehouse management system (WMS) job can signal a robotic counterbalanced stacker to pick up the pallet and move via the most efficient route to its assigned destination. For heavier loads or areas that require a tighter turn radius, a robotic reach truck may be the best choice.
For loose products not on a pallet, a robotic tow tractor with a cart can be programmed to position itself at the end of a conveyor or sorting table to receive products. Once a sensor or worker indicates the cart is full, the WMS system directs the tow tractor to shuttle that load to a final destination in a storage area or a shipping lane.
-
From receiving or staging to put-away in racking
The receiving docks at a high-volume warehouse must quickly move incoming loads to make room for the next arrivals. Once pallets are offloaded from trailers, inspected, labeled and scanned, the WMS triggers a job for a robotic reach truck to pick them up and move to a designated drop-off location in the racking. The WMS provides the exact pick-up spot and drop-off point so the robot accurately places the load in the right place. In fact, robots are more accurate and reliable than their manual counterparts when it comes to placing loads in the correct racking slot every time. Even in facilities without a WMS, some robotic trucks have specialized features to detect pallets in pre-programmed locations and create individual missions to put the loads in storage.
-
From raw goods storage to production line
When manufacturing line runs low on raw goods, fast replenishment is essential to preventing idle time that puts production targets in jeopardy. For a consistent supply, RLTs can be programmed for automatic deliveries or buttons can be installed for workers to make a manual request when parts are low. A robotic model then picks up the necessary material from bulk storage or racking and drops them off to feed the appropriate line.
This replenishment application is a common automation target because it keeps workers on the line and in controlled areas. Fewer workers moving widely around the facility keeps employees on task and helps mitigate the risk of injury associated with high traffic areas.
-
Picking tunnel replenishment
In this workflow, employees concentrate on building pallet orders in picking tunnels while robotic lift trucks handle replenishment – keeping products available to pick without disruption or delay. When a SKU runs low, the WMS triggers a request to replenish, and robotic reach trucks retrieve inventory from storage and bring it to the pick tunnel to support uninterrupted order fulfillment.
Different picking tunnels receive product differently, but some common applications for automation include depositing pallet loads onto flow racking from outside aisles, into single or double-deep racking outside the tunnel or in a bulk staging area outside. In most scenarios, the robotic truck remains outside the pick aisle to avoid impeding the manual or automated operation. If storage is located above the picking tunnel, a robotic reach truck can automatically pull pallets down from high-density vertical and double deep racking when a replenishment request is triggered.
By automating storage and replenishment work, operations can boost labor efficiency, with employees isolated from high-traffic areas and focused on the more challenging, engaging tasks of picking products and building pallets.
-
Cross Docking
Robotic lift trucks excel at performing with the speed and accuracy necessary in cross-docking applications. When a load is received and scanned into the WMS, a robotic end rider can retrieve up to four pallets at once and deposit them in the designated outbound locations.
Automation is especially valuable in this workflow because cross docking typically involves simple pallet moves. Assigning robotics to address this task allows operations to better utilize experienced operators for work that requires more complex maneuvering, rather that tying them up with basic point-to-point transport.
-
Receiving to staging, staging to outbound
A robotic end rider or counterbalanced stacker can be deployed to continually move loads from a dock zone or staging area to a racking lane, staging area or outbound location. These automated jobs are very simple for warehouses to implement because the lift trucks can detect pallets themselves, no full WMS integration required.
Leveraging robotics for these jobs can help operations reduce costs by making more efficient use of their labor – an especially effective cost reduction method considering labor is often a warehouse’s largest expense, typically consuming anywhere from 50-70% of warehouse operating budgets.
From automation plans to automation action
Having matured past the awareness stage, robotic lift trucks are now playing a major role in helping warehouses and manufacturers reduce operating costs, increase operational efficiency and avoid accidents. And as wages continue to rise, robotics are poised to reach 73% adoption in the next three to five years, according to MHI. In anticipation of future growth, many companies are planning ahead and choosing to invest in robotics – opting for earlier adoption rather than waiting until modernization becomes urgently necessary to keep up in an increasingly competitive market.
Robotics and automation experts at Gregory Poole are available to help you evaluate the right path to robotics for your operation.